Network Planning
Network Planning
Custom-fit industrial networks for your plants
Powerful networks as the basis for industrial digitalization
Whether it's ensuring trouble-free plant operation or seamlessly connecting multiple plant networks and network levels (OT/IIT/IT), the strength and reliability of your network are crucial for efficient (data) communication. So what is important when planning such a reliable industrial network?
Whether new or existing system: every network is different
Despite basic, common characteristics and functions, networks differ due to individual local requirements. For this reason, network solutions "off the shelf" must be adapted to the given applications and conditions in order to work reliably and efficiently.
As specialists for industrial communication networks, we support plant constructors and operators in planning, commissioning and operating modern industrial networks. In addition to the development of tailor-made network solutions for new plants, we offer the testing and optimization of existing plant networks.
Advantages of network planning (per user group)

Mechanical / plant engineering
(electrical construction)
Creating stable, cost-efficient networks
Challenges
> Designing modern, digitalized systems
> High cost pressure (competitors + customers)
Advantages of network planning
> Simplified commisioning (costs ↓)
> Lower service costs (costs ↓) already during warranty
> Stronger network infrastructure (mostly price neutral)

Plant operator
(maintenance / availability)
Networks as basis for maximum availability
Challenges
> Long-term profitability
> Maximize plant availibity
Advantages of network planning
> Basis for high system availability (more fault reserves, less error sources)
> Reduced maintenance costs (plannable, targeted measures)
> Lower or no remodeling costs

Plant operator
(IT / networking)
High-performance networking from OT to IT
Challenges
> Linking single networks (interference-free)
> Coordination of processes & components
Advantages of network planning
> Interference-free integration of different networks)
> Avoid infrastructure-related bottlenecks
> Lower or no remodeling costs
Independent Network Planning for Industry & Engineering
Until a few years ago, industrial plant networks, in particular, operated separately from one another (referred to as homogeneous networks). However, with increasing connectivity and modern monitoring solutions, maintaining this separation has become the exception rather than the norm. Consequently, most industrial networks today are heterogeneous or convergent networks. The interconnection of these modern industrial networks presents new challenges for planners and operators.
Evolving Criteria for Networks and Components
The complexity of industrial networks and their requirements is already evident in the initial planning stages, including the design of cable routes, industrial switches, and other network components. Gone are the days when network components from the same manufacturer as the used PLC could be simply installed. In the future, the selection of the appropriate network infrastructure components will primarily depend on the specific requirements of the individual segments as well as the overall network.
Tailored Network Planning instead of Costly Oversizing
Besides planning highly available industrial networks, the economic efficiency of these networks plays a crucial role in every phase. While generous oversizing may save time during network planning, the subsequent costs of materials and additional maintenance efforts often negate any initial savings. Therefore, our specialization lies in adapting industrial networks to meet the exact on-site requirements.
Your road to an optimized network
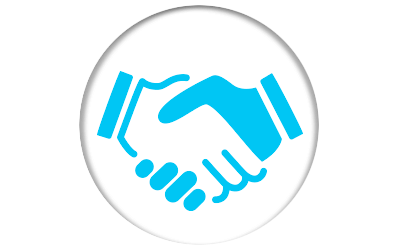
1 - The kick-off
Plant projects usually include a basic planning of the individual plant
and the network it contains. (ACTUAL)
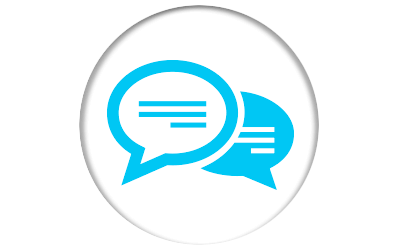
2 - The need for integration
The plant concept and the connected networks are checked by us. The
total required network performance is calculated. (TARGET)
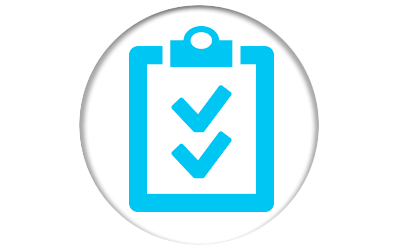
3 - The concept analysis
Based on the ACTUAL and TARGET status, we check the existing network
concept and the network components used for their suitability.
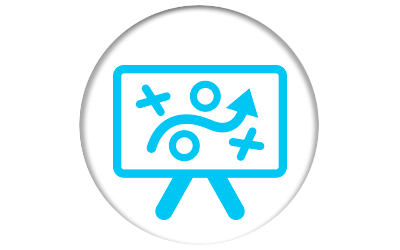
4 - The network planning
Based on all relevant requirements, network structure and components,
such as switches, are coordinated with each other.
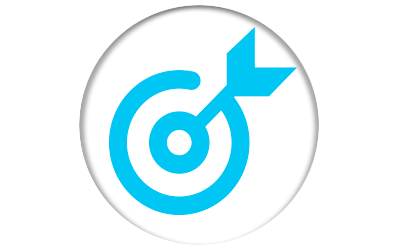
5 - The realization
In a final step, our experts accompany the implementation in an advisory
role or provide technical measurement support during the approval
process and commissioning.
Open OT networks securely - implement digitization efficiently
Anyone who wants to implement digitization projects, e.g. for energy management, inventory, condition monitoring or preventive maintenance concepts, knows the challenge: How do we get the data? The controls of machines and plants, the actual source of data, are often associated with self-contained networks and deny themselves any access from the outside. And this is by no means out of ill will, but because security and functional reliability are equated with isolation. However, anyone who wants to drive digitization projects forward efficiently should be able to use as much of the data as possible that is already available in machines. In this context, the network as a whole plays a central role. It must be well planned, sensibly segmented, optimized to the respective requirements, monitored and, above all, understood as such.
Today, however, a good 50% of digitization projects are doomed to failure (source: www.service-report-it.de) or are at least severely restricted or postponed for cost reasons because the resources to be expended on data acquisition exceed the planned budget. For example, in energy management, data is currently obtained using additional energy meters and queried via a separately installed network. These additional cost drivers make the project complicated, confusing and require additional maintenance and servicing.
Our adjusting screws for your success
> Plan OT networks according to the requirements of function and digitization
> Intensification of the exchange between operator and installer
> Highlighting data treasures - leveraging existing resources
> Bringing IIT and OT together without hurdles and barriers
> Determining responsibilities
> Establishment of access rules, their control and implementation
Achieve your digitization goals with us
Efficient Energy Management
> Avoidance of load peaks
> Identification of nominal current deviations
> Consumption forecasts for purchasing optimization
Permanent Condition Monitoring
> Reduction of throughput times
> Avoidance of downtimes
> Securing availability
Preventive
maintenance
> Avoiding breakdowns
> Guarantee network stability
> Be able to act before it is too late
Automated
inventory
> Overview of all assets and vulnerabilities
> Exposure of the security vulnerable devices
Industrial networks in transition - a short explanation
Planned implementation instead of complicated temporary solutions
Whether you have an established facility or a new one, say goodbye to transitional solutions and outdated procedures. Our expert guidance will show you how to optimize your plant networks, unlocking economic benefits and reducing maintenance costs for tomorrow.
> Data volume in individual plant networks is constantly increasing
Machines and plants are becoming increasingly complex, equipped with more sensors and data sources. Despite the growing data volume (network load ↗), it remains crucial to transport prioritized process data seamlessly and in real-time, without any losses.
> Exchange of process data across plants (plant networking)
If several systems are operated in parallel, they often have to exchange comprehensive process data. In addition to ensuring smooth data exchange, these connections must meet all the requirements for network performance and security.
> Network communication has evolved to be more versatile and expansive
In addition to pure process communication (e.g., only PROFINET), modern industrial networks must also be able to handle various communication protocols and applications. Unplanned networks can quickly reach their limits when these networks are exchanging prioritized process data and additional data from connected network cameras, user panels, and other devices.
What does this mean for operators of industrial plants?
For both existing and new plants, machine networks must be prepared to ensure smooth operation and secure data exchange. By doing so, you can establish a solid foundation for the digital transformation of your machine processes. This proactive approach helps avoid costly structural adjustments and maintenance procedures during the operating phase. If this sounds interesting to you, consider planning your networks with InduSol America.
What does this mean for industrial plant manufacturers?
Industrial plant networks must be able to adapt to changing requirements and the growing
need for connectivity. By engaging in targeted network planning, you can proactively identify
potential weak points in the structure and infrastructure. This allows for simplified commissioning,
even amidst increasing complexity.
Request a consultation
Do you have any questions or would you like advice from our experts? Simply send us your enquiry - conveniently online.