What is PROFINET?
PROFINET is a universal, Ethernet-based communication network that can be used in all areas of automation technology. Speedy vertical and horizontal data exchange across all levels – including the corporate control level – is the foundation for successful systems concepts.

Like PROFIBUS, PROFINET distinguishes between acyclical and cyclical data communication (RT – Real Time) and additionally supports fast I/O communication (IRT – Isochronous Real Time). This is done while retaining the familiar design with a cyclical transfer of peripheral data between the field devices (IO devices) and the process image in the IO controller. This results in a high degree of flexibility because update rates are scalable (see Fig. 5).

PROFINET describes a device model that is based on the principles of PROFIBUS and consists of slots and groups of IO channels (sub-slots). The technical characteristics of the field devices are described by a so-called GSD (General Station Description) that is based on XML.
Data in PROFINET networks is highly varied. Besides prioritized, cyclical PROFINET I/O data, acyclical data (e.g. TCP/ IP, diagnostic messages or SNMP requests) can be transmitted (see Fig. 6).
Network topologies in PROFINET derive from the requirements of the systems to be networked. The most common structures are star, line, tree and ring-shaped. In practice, systems usually are a mix of the above structures. They can be implemented either with copper or fiber-optic cables.


PROFINET Design Guideline and Commissioning Guideline
The extensive options for configuration and utilization of a network necessitate careful planning and practice- oriented commissioning of the system. The user organization PROFIBUS & PROFINET International (PI) has defined quality criteria for planning, acceptance and commissioning, as well as the metrological evaluation of a network in its latest Design and Commissioning Guideline. It is intended as a guideline for all persons and organizations involved in the planning, installation, operation and maintenance of such systems.
In the planning stage, network utilization should be considered in addition to structure. For this purpose, it is important to know the relationships between update rate, line depth and network structure (see PROFINET Network Planning). Practical planning tools like PROnetplan by Indu-Sol can be used to display such relationships in an interactive graphic to avoid weak spots.
Moreover, it is useful to define the requirements for IO devices in advance. The categorization in Conformance Classes (CC-A, CC-B, CC-C) is a useful aid to users when selecting devices that have no more than the required functionality. Requirements include simultaneous access to devices by several controllers (IO controllers), support for media redundancy, detection of topology information in the network, device exchange without repeated use of a parameterization device, as well as applications with very short cycle times and low variation.
The selection and placement of network components in the network structure depends on the performance of the devices. It is described by the net load classes.
The years of experience with fieldbus technology have shown that the extensive diagnostic options of controllers in the area of device diagnostics should be expanded by an additional measurement to verify the quality of communication. The measurements serve as dual purpose, namely a description of the PROFINET network on the one hand and ensuring operational reliability on the other. Special attention should be paid to assuring the quality of the line connections (test when plant is stopped) as well as the transmission during operation.
Watch "PROFINET - The Movie":
Keep learning:
PROFINET
PROFINET in the context of Industry 4.0PROFINET Network Planning
ServiceTool
How to use the Indu-Sol ServiceTool to identify the IP of PROFINET devicesPROFINET-INspektor®
How to configure ports in the PROFINET-INspektor®How to set PLC as Master in the PROFINET-INspektor®
How to set-up automatic topology scanning in the PROFINET-INspektor®
How to set-up automatic Switch scanning in the PROFINET-INspektor®
How to get reports and alarms from the web interface of the PROFINET-INspektor®
How to make a manual snapshot in the PROFINET-INspektor®
PROFIBUS
What is PROFIBUS?Learn how to test and diagnose PROFIBUS systems in 5 steps
PROFINET Brochure
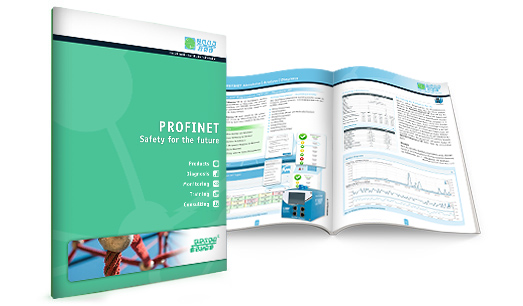
PROFINET - Safety for the future explains technological coherences in detail that are based on the latest valid standards and guidelines.
Download